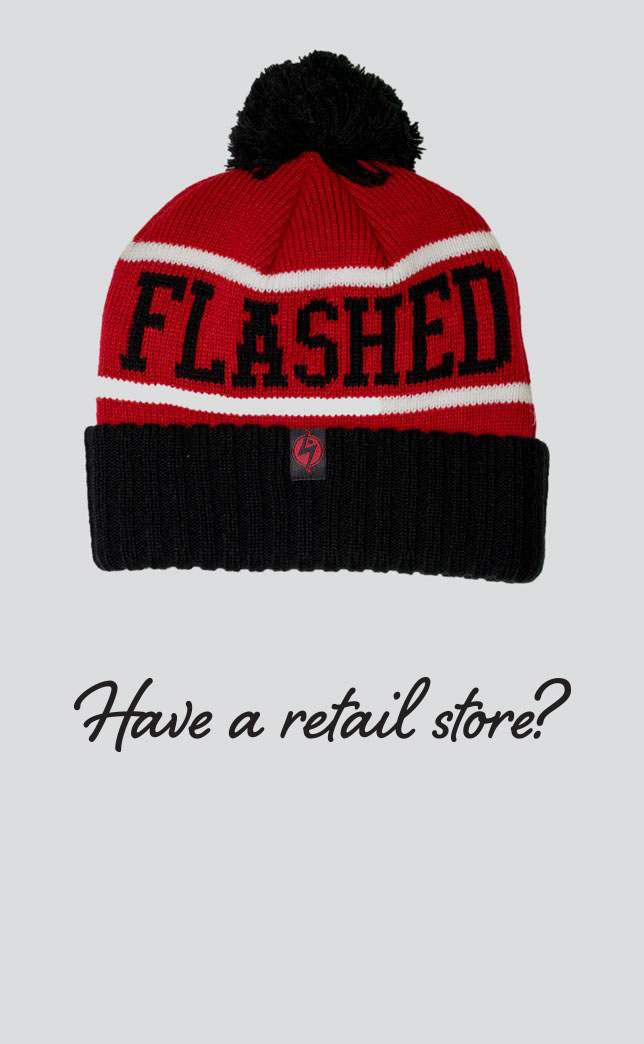
TALK TO US ABOUT WHOLESALE BUYING
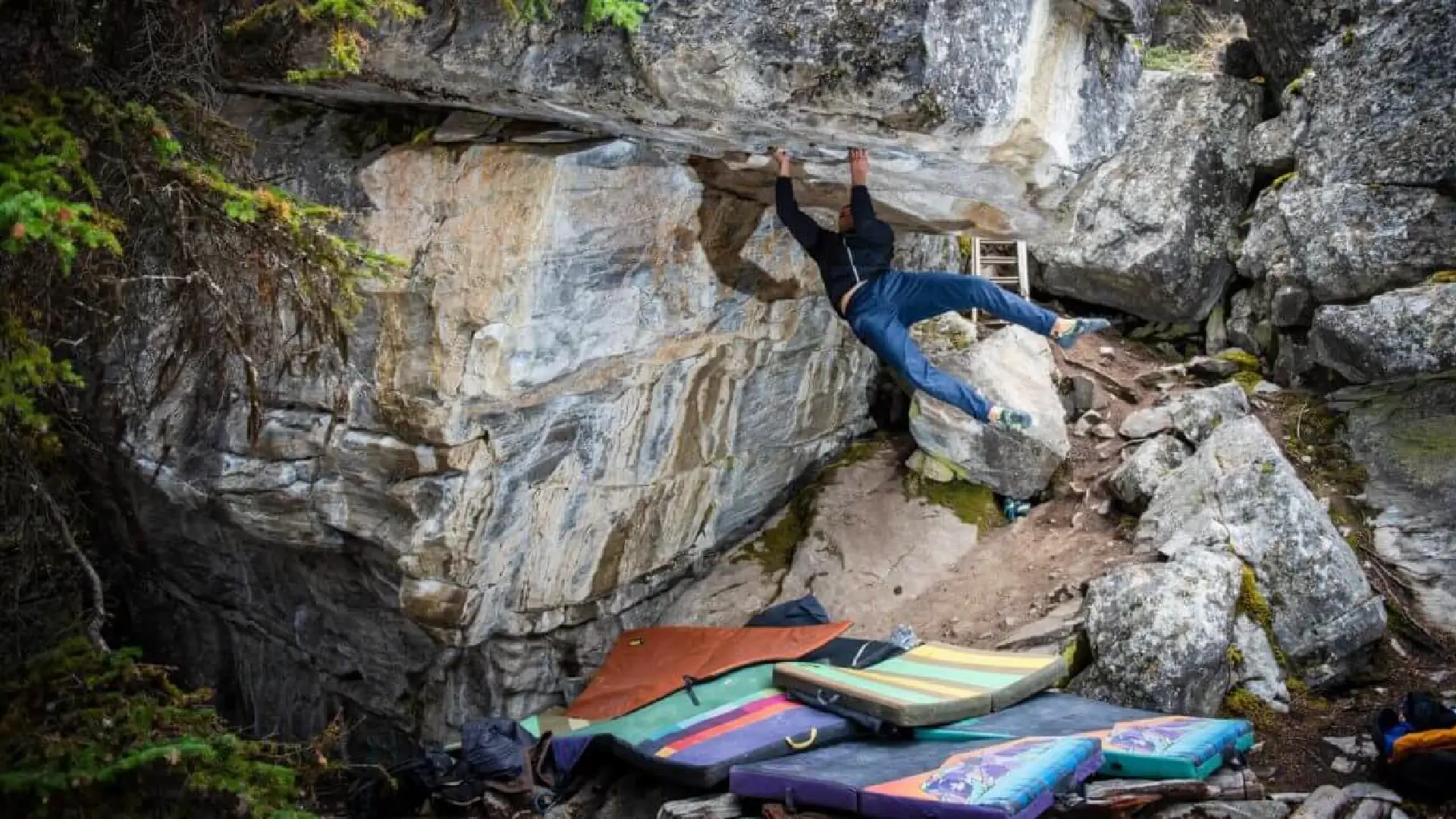
IT’S WHAT WE’RE KNOWN FOR...
The New Standard in Quality + Innovation
Curiosity is the root of all knowledge and success here at Flashed! We analyze problems with a scientific approach, reasoning what causes them. The iterative process to solve these issues may take time but it’s worth it in order to create innovative products that adapt to any terrain indoors or out!
EVOLUTION
For the last two and a half decades, we’ve been there as bouldering pads morphed from duct-taped sofa cushions into refined landing systems. River rock, chipped rubber, and even moveable pads were commonplace not that long ago in climbing gyms; now gym padding is clean uniform attractive easy to maintain with a dialed-in impact attenuation response capable of handling hundreds or thousands of climbers daily. Adapting and evolving to these changing demands has always been essential for us here at Flashed where we have led the industry by setting the standard.
It’s been a wild ride so far and we look forward to taking things forward from here. Here is a short timeline description of our story:
Continuous Development
Nothing stays the same, everything is always on the move, shifting, evolving. Over our 27yr history, Flashed has always strived to be at the forefront, or even ahead, of that leading edge.
Demands on products, methods of application, a growing climbing community: these are always changing and our commitment is to keep on top so you can trust any product that has our name on it. Both today and into the future.
Materials Research
For any product, it simply has to work, and work well. Along with intelligent design and proper field testing the dependability of a product is based on the materials used. For this reason we spend an inordinate amount of time researching materials to get this right. This approach permeates all of our products and we trust you’ll recognize the difference.
Padding
The majority of climbing padding consists of polyethylene (PE) and polyurethane (PU) foams. PE foam is the harder closed-cell product used as a force dispersion layer (like gymnastic carpet bond) while PU foam is the open cell soft and squishy material used in bouldering pads and under route flooring. Although data is available from other industries, climbing is a dynamic impact sport and specialized equipment is necessary.
Chalk Research
Our story was born with the chalk ball in 1995, but we didn’t stop there. Over the last two decades, we’ve innovated, tested, and strove to create the best-performing chalk on the market. Recently, we teamed up with UBC to devote substantial research to climbing chalk.
Our inquisitiveness is grounded in a genuine desire to advance the sport. As dedicated climbers, we recognize the pivotal role chalk plays in performance. But our work doesn’t stop at improving grip or managing moisture—we’re investigating the fundamental science behind chalk.
By exploring what makes chalk truly effective, we aim to optimize its properties for both performance and environmental responsibility. Our ambition is to produce chalk that’s gentler on the planet without sacrificing quality. We invite you to join us on this path of innovation and discovery as we push the boundaries of what’s possible in climbing.
Learn more about our Chalk Research Initiative
Accelerometer
Going back to 2004, bouldering pads were described as having the best dual-density foam on the market. There was no way to quantify these claims until Flashed introduced the test missile Drop Tester and we started putting a numerical value to impacts. This uses a headform missile for drop tests with a 3-axis accelerometer inside. Our focus was not on the padding, as some manufacturers focuses using load cells beneath the pads, but rather on the impacting missile itself.
Now in 2023, Flashed has since upgraded to the Triax 2015 testing equipment and is able to perform head impact drops at nearly any gym height. As gym user visits increase and more people are attracted to our sport, we want to ensure the information and tools are available to make informed choices.
Dynamic Fatigue
Once we understand what impacts are experienced by the test missile the next natural question is durability. Performance and Durability go hand in hand and the input factors are related. Durability is affected by three main characteristics: density, resiliency, and compression firmness. Generally, the more dense (heavy) the foam is, the longer it will last. Higher resilient foams will maintain support levels for longer. Additionally, the more stiff it is, the more support it provides. Certainly the stiffness also affects the feeling of impact on the climber.
To understand the specifics of each foam type we needed to evaluate how the impact changes over time with respect to both density and compression. The Dynamic Fatigue Tester (DFT), was developed to raise the test weight missile up to a set height required to compress the foam 75%. An internal Accelerometer measures the drop impact in g-force and is then graphed over 1000 drops to give us a trendline. By doing this with various densities and compressions of PU foam we can better understand and compare padding.
;
MOFO
The Multiple Overhead Fall Operator (MOFO) looks at testing a complete padding system, not just individual foam layers like the DFT. The MOFO uses single-axis CNC controls to performs 1000s of drop at heights up to 18ft or larger. Although the DFT is limited to just the weight of the test missle itself , the MOFO is made to allow for additional added weights.